Case Study: Optimizing efficiency: How automated mine shaft inspections reduce downtime
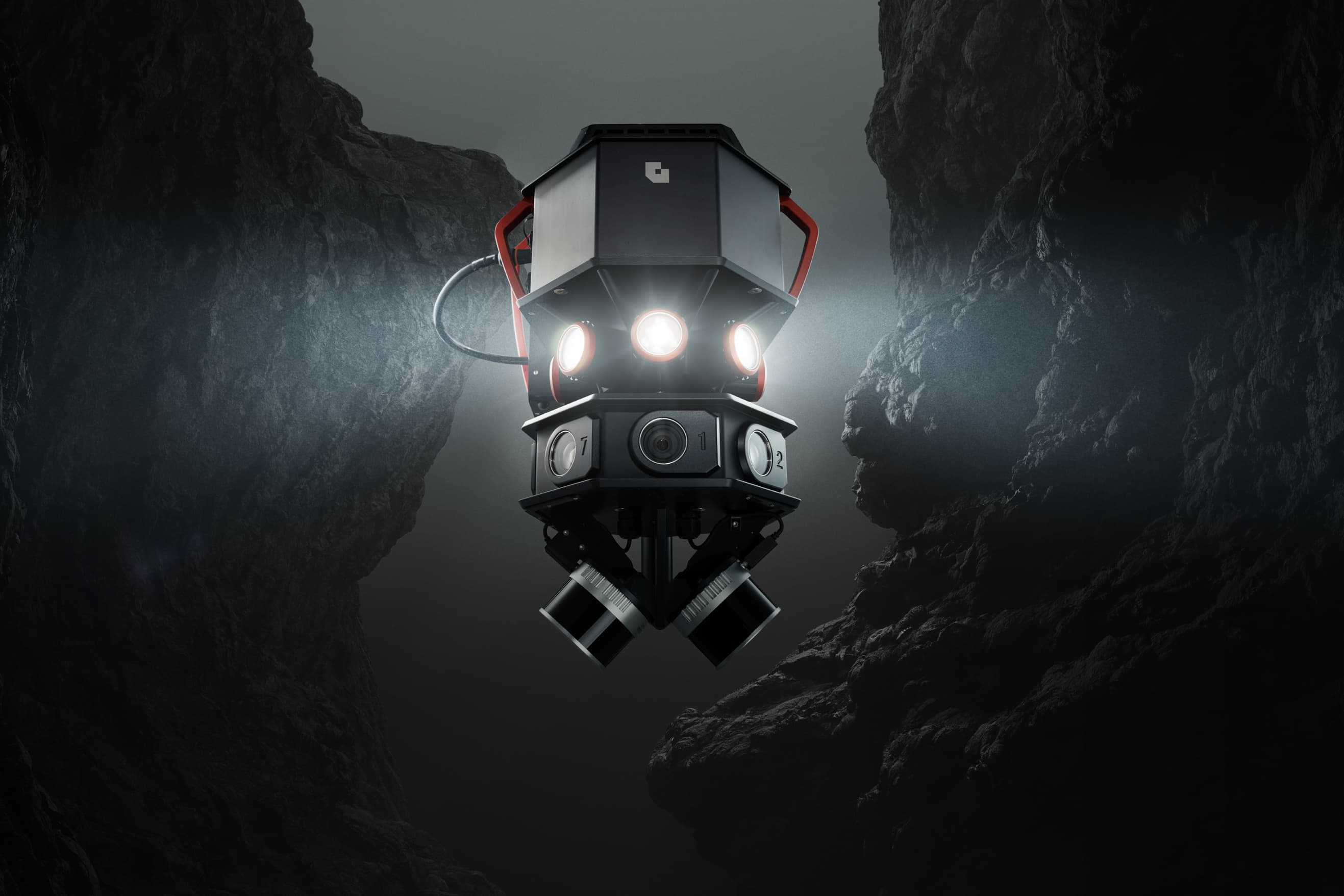
In the world of mining, efficiency isn’t just a goal — it's the cornerstone of sustainable and profitable operations (Dold, 2020). Mine shaft inspections are an important component of mining efficiency since their enforcement is inherent to operations. However, these inspections often result in significant downtime, directly impacting productivity and operational costs (Harish Kumar, Choudhary & Murthy, 2020). This article explores how the advent of automated mine shaft inspection technologies is revolutionizing the mining industry by significantly reducing downtime, highlighting the common causes of mine shaft closures and illustrating the role of automation in mitigating these challenges.
The Cost of Downtime in Mining Operations
Downtime in mining operations can be attributed to a variety of factors, ranging from equipment failure and maintenance to safety inspections and environmental conditions. Each minute a mine shaft is non-operational not only incurs direct financial losses, but also delays in production schedules. Among the most common reasons for mine shaft downtime, safety inspections stand out both for their unavoidability, their frequency and their impact on operations. While these inspections are typically planned, they translate into thousands of dollars per hour in downtime to the mining industry (Maxontana, M., 2022). Additionally, unplanned downtime, which may arise from sudden equipment failures or emergency safety concerns, can lead to exponentially higher costs, as witnessed in Impala’s shaft accident which resulted in a 20% loss in revenue and a 3-month shutdown (Williams, 2024)
What are the Most Common Causes of Mine Shaft Downtime?
- Equipment Failure: Breakdowns of drilling rigs, conveyors, ventilation systems, and other critical machinery can force to stop operations until repairs are made (Maxontana, M., 2022).
- Maintenance: Scheduled maintenance is essential for the longevity and efficiency of mining equipment, but it also requires pausing operations.
- Safety Inspections: Regular inspections are mandatory to ensure the mine complies with safety regulations and to protect workers from hazards. Traditional methods of inspection can be time-consuming, often requiring partial or full cessation of operations.
- Environmental Factors: Natural events such as flooding, seismic activity, or extreme weather can compromise mine safety and necessitate temporary closures for assessment and mitigation.
- Regulatory Compliance: Compliance with mining regulations may require periodic shutdowns for audits and inspections to ensure operations meet legal and environmental standards.
Preventing Unplanned Downtime with Automation
Technologies that enable regular automated data-oriented inspections of mine shafts play a crucial role in preventing unplanned downtime. Automated mine shaft inspections mark a significant shift away from the traditional methods by reducing the risk of incidents but also shortening downtime when such unexpected issues occur.
Unplanned downtime can have devastating effects on productivity and economic efficiency (Boltstress, 2018). It often occurs without warning, due to equipment malfunctions or unforeseen safety hazards, leading to abrupt halts in production. Automated inspection technologies like the Lazaruss 3D scanner address this issue directly by providing on-demand surveillance and analysis, ensuring that potential failures are identified and addressed before they might disrupt operations.
What are the Benefits of Automated Inspections in Preventing Unplanned Downtime?
- Speed: Automated inspections are significantly faster than manual methods, reducing the shutdown time associated with the inspection. Drones and robotic systems can swiftly cover extensive areas of a mine, delivering critical data that helps in making operational decisions.
- Safety: Using automated systems minimizes human exposure to potentially dangerous mine environments (Green et al., 2010). This reduction in human involvement not only enhances safety but also decreases the likelihood of accidents that could lead to unplanned downtime.
- Comprehensive Data: These systems gather extensive data, including high-resolution images and detailed structural analyses. This wealth of information is crucial for both immediate responses and for establishing long-term monitoring systems that can alert operators to issues before they escalate into costly problems.
- Predictive Maintenance: AI-driven predictive maintenance is perhaps one of the most significant advantages of automated inspections. By analyzing data over time, AI algorithms might forecast when and where maintenance should occur, scheduling it for optimal times and thereby minimizing unexpected interruptions.
- Consistency: Automated systems provide a regular, objective assessment of mine condition, reducing human error and the variability of assessments that can lead to oversights and unplanned downtime.
How to Implement Automated Inspections for Mine Shafts with the Lazaruss 3D Scanner?
To effectively implement automated inspection technologies for mine shafts, mine operators must embrace the transition from more traditional inspections to advanced automated systems such as the Lazaruss 3D scanner.
The initial implementation step involves a comprehensive analysis of the geometry of the mine shaft to ensure that the acquisition parameters and output meet the operator’s requirements. Following this analysis, our team of experts will train people on-site so that they can easily and efficiently use the device. The system is designed for fast and easy integration into the mine’s operation, using a proprietary attach system that adapts to any cable size and requires only a few minutes to install.
Once installed on the cable, the Lazaruss 3D scanner operates with virtually any operator intervention. It delivers on-demand, high-resolution data that allows mine operators to make informed decisions quickly, thereby reducing downtime and enhancing operational efficiency.
Demonstrating a Reduction in Downtime
More and more emerging case studies highlight the effectiveness of automated mine shaft inspections in reducing unplanned downtime. For example, Point Laz’s partners that have integrated their solution have been able to assess the alignment of the guides in the mine shaft and to perform predictive maintenance at locations identified by the Lazaruss scanner. Other users have been able to detect the early formation of cracks in the concrete and intervene before any structural damages occur by using the complementarity of the 3D measurements and the visual information available.
By moving towards automated inspection technologies, mining operations can significantly mitigate the risks associated with unplanned downtime. The integration of such technologies is rapidly proving to be indispensable for modern mining operations, striving to maintain high efficiency and productivity in an increasingly challenging industry environment.
Conclusion
The adoption of automated mine shaft inspection technologies such as the Lazaruss 3D scanner offers a promising solution to one of the mining industry's perennial challenges: reducing downtime while also improving miners safety. By harnessing the power of AI, and data analytics, mines might not only minimize the operational disruptions caused by traditional inspection methods but also enhance their overall safety and efficiency. As the industry continues to evolve, the integration of such technologies will no doubt help shape the future of mining; unlocking efficiency, and ensuring the sustainability of operations for years to come.
References
Benecke, N., Hancock, P., & Weber, M. (2016). Latest developments in the practice of shaft inspection. Mine Surveying, 12-16. https://www.minesurveyors.com.au/files/ISM2016/Proceedings/Section3/1_N_Benecke.pdf
Boltstress (2018). Downtime Cost in a Mining Industry. https://www.boltstress.com.au/blog/webpage-content/downtime-cost-in-a-mining-industry
Dold, B. (2020). Sourcing of critical elements and industrial minerals from mine waste – The final evolutionary step back to sustainability of humankind? Journal of Geochemical Exploration, 219. https://doi.org/10.1016/j.gexplo.2020.106638
Green, JJ, Bosscha, P, Candy, L, et al. 2010. n can a robot improve mine safety? 25th International Conference on CAD/CAM, Robotics and Factories of the Future (CARsFOF), CSIR International Convention Centre, Pretoria, July 13-16, 2010, pp. 13. https://www.researchgate.net/publication/228412143_Can_a_robot_improve_mine_safety
Maxontana, M. (2022, July 21). Mitigating the cost and dangers of downtime in mining. Insights by Adcorp. https://insights.adcorpgroup.com/mitigating-the-cost-and-perils-of-downtime-in-mining
N. S. Harish Kumar, R. P. Choudhary & Ch. S. N. Murthy. (2020) Model based reliability analysis of shovel - dumper system's mechanical failures used in the surface coal mine: a case study. Safety and Reliability 39:3-4, pages 215-229.
Williams, G. (2024) Impala's Shaft 11 set to reopen, operations resume after tragic incident. Mining Magazine. https://www.miningmagazine.com/operations/news/4169659/impalas-shaft-set-reopen-operations-resume-tragic-incident
Embrace the future of mining with Point Laz technologies. By investing in automation, your operation should see a reduced downtime, improved safety, and increased efficiency, paving the way for a more profitable and sustainable future. Explore the possibilities today and take a step towards transforming your mining operations.