The Critical Role of Automated Inspections in Enhancing Mine Shaft Safety
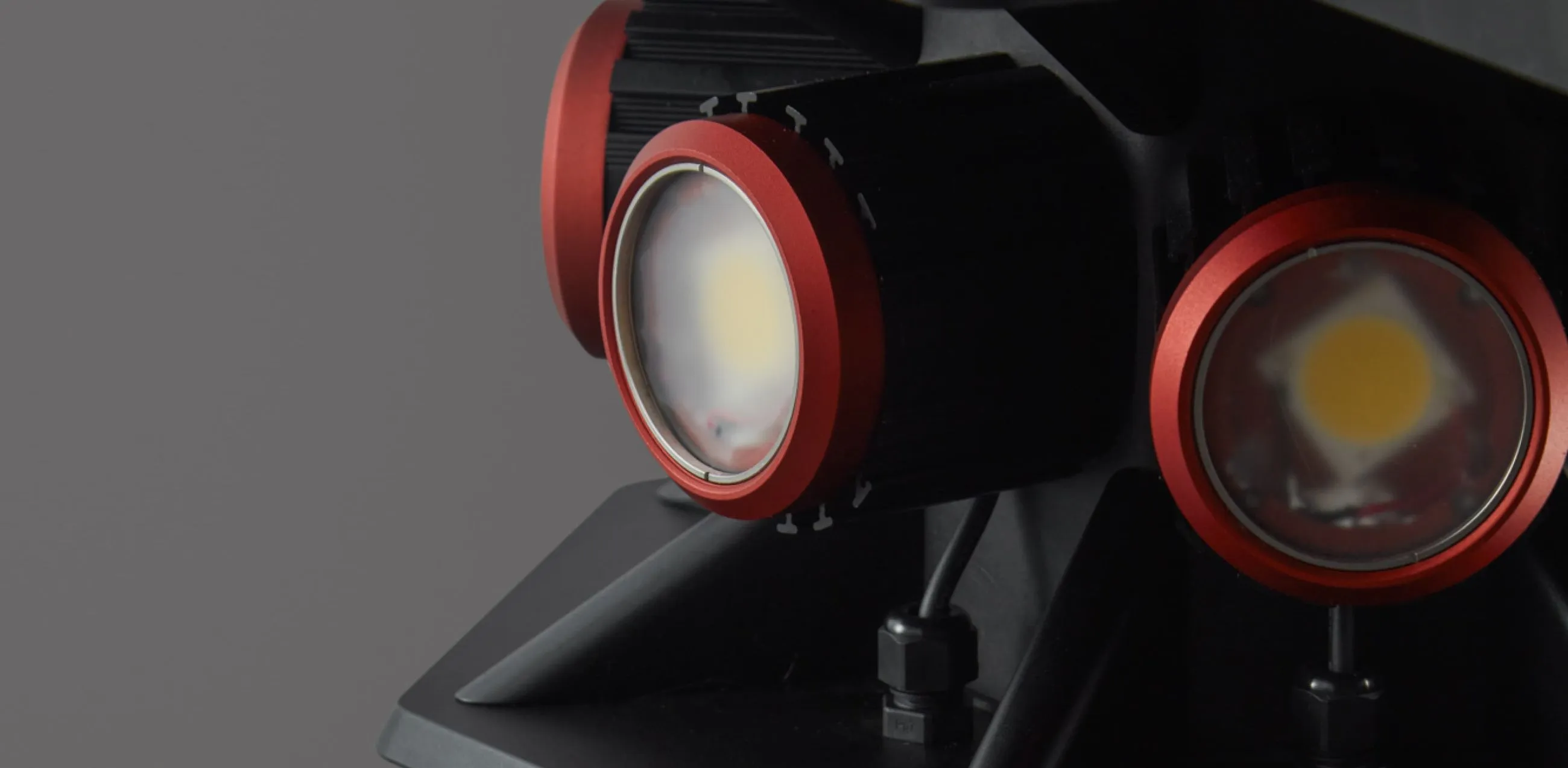
Mining operations inherently involve risks, especially within the ever-changing, constrained and often unpredictable environment of a mine. Factors such as dust, humidity, gases and dirt may alter the integrity of one of the main risk elements, the mine shaft (Benecke et al., 2016).
Ensuring the safety and integrity of these shafts is not just a regulatory requirement, but a fundamental necessity to protect the health and lives of miners and the operational continuity of mines. Recent advancements in technology, particularly through innovative solutions like automated inspections, have revolutionized how mine shaft safety and inspections are approached. In this article, we will look at some of the most common safety challenges and how pioneering solutions like our Lazaruss 3D scanner help improve those.
Unveiling the Hazards: Why Mine Shaft Safety is Paramount
It’s no surprise that the mining industry continues to experience numerous accidents that are directly linked to mine safety failures, most often resulting from human errors. In fact, the mining industry has been described as one of the most hazardous industries (Qadri et al., 2021). Incidents can range from collapses due to structural failures, to hazardous gas leaks, flooding and failure of the shaft lining, all of which pose significant threats to miner safety and mine productivity (Lecomte et al., 2012).
Moreover, visual inspections of mine shafts involve considerable risks. Not only do miners put themselves at risk while navigating those deep and mobile structures, but the analyses that result from these inspections are also prone to human error, which puts every worker present in the mine shaft at risk.
By recognizing these challenges, it becomes evident why prioritizing rigorous mine shaft inspections is crucial since it directly impacts the overall safety of mining operations and the well-being of the workforce.
The recent events that occurred at Impala’s Rustenburg mine in South Africa, which caused injuries to 75 people and 11 fatalities after a winder rope had broken is a perfect example of a mining tragedy directly linked to the mine’s safety issues having enormous consequences (Mining Technology, 2023).
Revolutionizing Mine Shaft Inspections with the Lazaruss 3D Scanner
Point Laz’s technology represents a significant leap forward in mining safety practices. The Lazaruss scanner automates the inspection process, effectively eliminating the need for humans to enter potentially hazardous zones. This not only reduces the risks associated with traditional visual inspection methodologies but also enhances the accuracy and reliability of the assessments.
With its survey-grade LiDAR technology and high resolution imaging devices, the Lazaruss scanner creates a detailed 3D model of the mine shaft. This model provides comprehensive data on the condition of the shaft, detecting even the smallest anomalies that could indicate potential risks, such as cracks or structural weaknesses. This level of detail ensures that potential issues can be addressed before they pose a real threat to mine shaft safety or efficiency (Imam et al., 2023).
The Benefits of Automated Mine Shaft Safety Inspections
By reducing the need for miners to conduct visual inspections and providing data from the mine shaft conditions, automated inspections significantly improve miner safety and reduce the risks of on-the-job accidents and injuries (Imam et al, 2023). We believe that our proactive approach to mining safety helps foster a workplace culture that prioritizes an accident-free work space and encourages productivity without compromising on safety.
Additionally, automated inspections contribute to improve operational efficiency. With Lazaruss, inspections can be conducted quicker and comprehensively while minimizing disruptions to mining operations. This easy-to-use and fast-to-deploy type of monitoring allows for the reliable identification and rectification of potential issues, thus minimizing downtime and maintenance costs. It also allows for precise engineering solutions based on a precise 3D model of the situation to survey.
The data-driven insights provided by Lazaruss also aid in long-term mine planning and development strategies. By having a clearer understanding of the mine shaft conditions, mining companies can make more informed decisions that optimize their operations and ensure environmental compliance.
Take Action for a Safer Mine
Mining companies looking to enhance their safety protocols and operational efficiency should consider the notable benefits of automated mine shaft inspections via 3D modelling renders, which are now becoming vital to ensure proper safety (LeCras et al., 2009).
The Lazaruss scanner exemplifies the benefits of such technology by offering a robust solution to what we believe remains one of the industry's most important challenges.
For more detailed specifications and to understand how the Lazaruss scanner can transform your mining operations, read more about its specifications. Embrace the future of mining with technology that not only protects but propels your operations forward.
References
Benecke, N., Hancock, P., & Weber, M. (2016, September). Latest developments in the practice of shaft inspection. In Proceedings of the XVI Congress of the International Society of Mine Surveying (ISM), Brisbane, Australia (pp. 12-16).
Imam, M., Baïna, K., Tabii, Y., Ressami, E. M., Adlaoui, Y., Benzakour, I., & Abdelwahed, E. H. (2023). The future of mine safety: a comprehensive review of anti-collision systems based on computer vision in underground mines. Sensors, 23(9), 4294.
Lecomte, A., Salmon, R., Yang, W., Marshall, A., Purvis, M., Prusek, S., ... & Niharra, A. M. (2012, April). Case studies and analysis of mine shafts incidents in Europe. In 3. International Conference on Shaft Design and Construction (SDC 2012) (p. NC).
LeCras, J., Paxman, J., Saracik, B., & Jarosz, A. (2009). An inspection and surveying system for vertical shafts. In Proceedings of the 2009 Australasian Conference on Robotics & Automation. Australian Robotics and Automation Association.
Mining Technology (2023). Retrieved on July 2nd 2024 at: https://www.mining-technology.com/news/impala-rustenburg-accident-11-dead/
Qadri, I., Muneer, A., & Fati, S. M. (2021). Automatic robotic scanning and inspection mechanism for mines using IoT. In IOP conference series: Materials science and engineering (Vol. 1045, No. 1, p. 012001). IOP Publishing.
By integrating advanced solutions like Lazaruss, we can ensure that the mining industry continues to evolve in a direction that prioritizes the safety of its workforce above all else.