Optimiser l'efficacité : Comment les inspections automatisées des puits de mine réduisent les temps d'arrêt
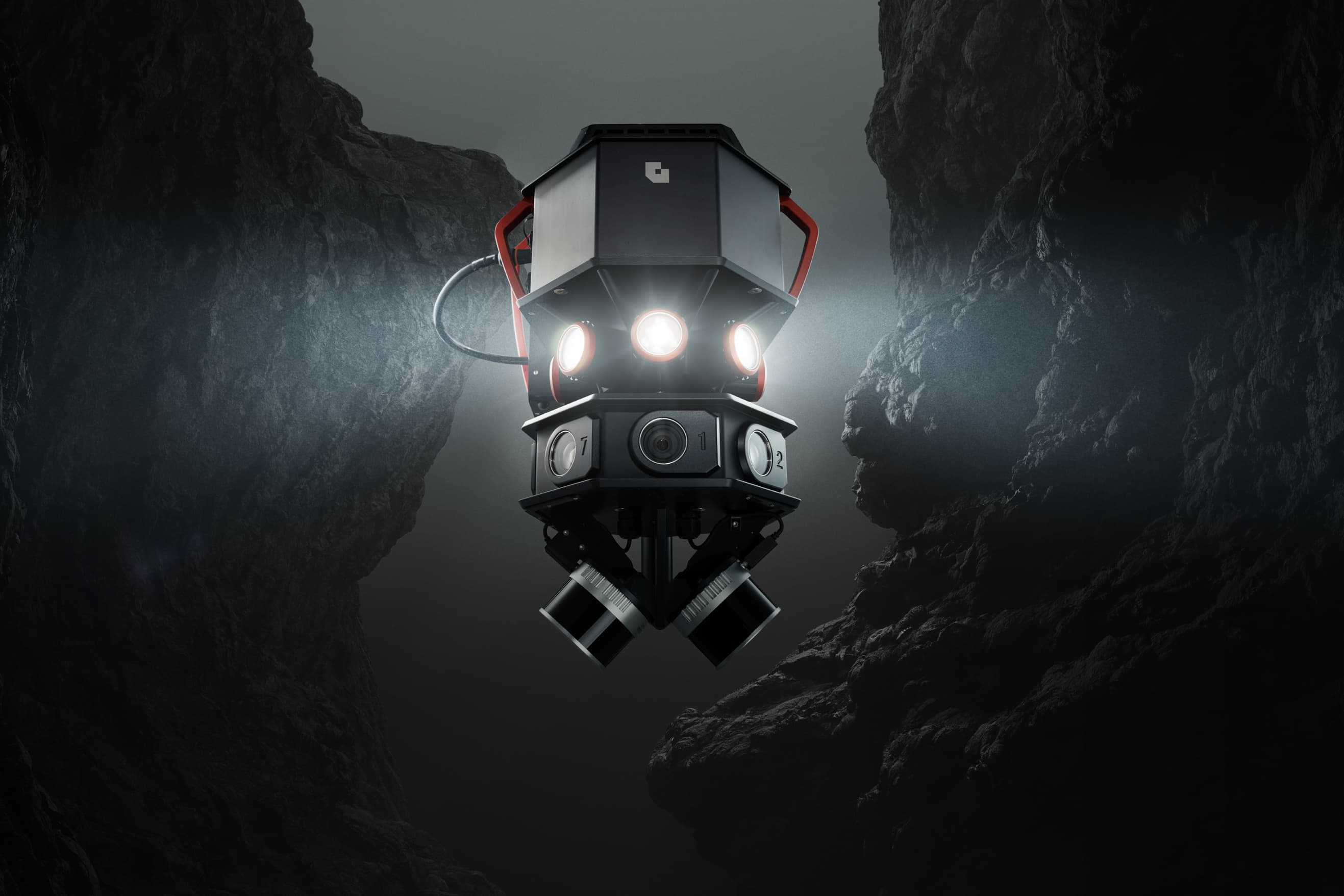
Dans le monde de l'exploitation minière, l'efficacité n'est pas seulement un objectif, c'est la pierre angulaire d'une exploitation durable et rentable (Dold, 2020). Les inspections des puits de mine sont un élément important de l'efficacité minière, car leur exécution est inhérente aux opérations. Cependant, ces inspections entraînent souvent des temps d'arrêt importants, ce qui a un impact direct sur la productivité et les coûts opérationnels (Harish Kumar, Choudhary & Murthy, 2020). Cet article explore la manière dont l'avènement des technologies d'inspection automatisée des puits de mine révolutionne l'industrie minière en réduisant de manière significative les temps d'arrêt, en soulignant les causes courantes de fermeture des puits de mine et en illustrant le rôle de l'automatisation dans la réduction de ces défis.
Le coût des temps d'arrêt lors des opérations minières
Les temps d'arrêt pour les opérations minières peuvent être attribués à divers facteurs, allant de la défaillance et de l'entretien des équipements aux inspections de sécurité et aux conditions environnementales. Chaque minute pendant laquelle un puits de mine n'est pas opérationnel entraîne non seulement des pertes financières directes, mais aussi des retards dans les échéanciers de production. Parmi les raisons les plus courantes de l'arrêt d'un puits de mine, les inspections de sécurité se distinguent à la fois par leur caractère inévitable, leur fréquence et leur impact sur les opérations. Bien que ces inspections soient généralement planifiées, elles se traduisent par des milliers de dollars par heure de temps d'arrêt pour l'industrie minière (Maxontana, M., 2022). En outre, les temps d'arrêt non planifiés, qui peuvent résulter de défaillances soudaines de l'équipement ou de problèmes de sécurité urgents, peuvent entraîner des coûts exponentiellement plus élevés, comme en témoigne l'accident du puits d'Impala, qui a entraîné une perte de revenus de 20 % et une fermeture de trois mois (Williams, 2024).
Quelles sont les causes les plus fréquentes du temps d'arrêt d'un puits de mine ?
- Défaillance de l'équipement : Les pannes d'appareils de forage, de convoyeurs, de systèmes de ventilation et d'autres machines essentielles peuvent obliger à arrêter les opérations jusqu'à ce que les réparations soient effectuées (Maxontana, M., 2022).
- Maintenance : L'entretien régulier est essentiel à la longévité et à l'efficacité de l'équipement minier, mais il nécessite également l'interruption des opérations.
- Inspections de sécurité : Des inspections régulières sont obligatoires pour s'assurer que la mine respecte les règles de sécurité et pour protéger les travailleurs contre les dangers. Les méthodes traditionnelles d'inspection peuvent prendre beaucoup de temps et nécessitent souvent un arrêt partiel ou total des opérations.
- Facteurs environnementaux : Les événements naturels tels que les inondations, l'activité sismique ou les conditions météorologiques extrêmes peuvent compromettre la sécurité des mines et nécessiter des fermetures temporaires à des fins d'évaluation et d'atténuation.
- Respect de la réglementation : Le respect des réglementations minières peut nécessiter des fermetures périodiques pour des visites et des inspections afin de s'assurer que les opérations respectent les normes légales et environnementales.
Prévenir les arrêts imprévus grâce à l'automatisation
Les technologies basées sur des données, qui permettent des inspections automatisées et régulières des puits de mine, jouent un rôle crucial dans la prévention des temps d'arrêt non planifiés. Les inspections automatisées des puits de mine marquent un changement significatif par rapport aux méthodes traditionnelles en réduisant le risque d'incidents, mais aussi en raccourcissant les temps d'arrêt lorsque de tels problèmes inattendus se produisent.
Les temps d'arrêt imprévus peuvent avoir des effets dévastateurs sur la productivité et l'efficacité économique (Boltstress, 2018). Ils se produisent souvent sans avertissement, en raison de dysfonctionnements de l'équipement ou de risques de sécurité imprévus, ce qui entraîne des arrêts soudains de la production. Les technologies d'inspection automatisées telles que le scanner 3D Lazaruss s'attaquent directement à ce problème en fournissant une surveillance et une analyse à la demande, garantissant que les défaillances potentielles sont identifiées et abordées avant qu'elles ne perturbent les opérations.
Quels sont les avantages des inspections automatisées pour prévenir les temps d'arrêt imprévus ?
- Rapidité : Les inspections automatisées sont nettement plus rapides que les méthodes manuelles, ce qui réduit le temps d'arrêt associé à l'inspection. Les drones et les systèmes robotisés peuvent couvrir rapidement de vastes zones d'une mine et fournir des données critiques qui aident à prendre des décisions opérationnelles.
- Sécurité : L'utilisation de systèmes automatisés minimise l'exposition humaine à des environnements miniers potentiellement dangereux (Green et al., 2010). Cette réduction de l'implication humaine renforce non seulement la sécurité, mais diminue également la probabilité d'accidents susceptibles d'entraîner des temps d'arrêt non planifiés.
- Données complètes : Ces systèmes recueillent de nombreuses données, notamment des images à haute résolution et des analyses structurelles détaillées. Cette quantité d'informations est cruciale à la fois pour les réponses immédiates et pour la mise en place de systèmes de surveillance à long terme qui peuvent alerter les opérateurs sur des problèmes avant qu'ils ne se transforment en problèmes coûteux.
- Maintenance prédictive : La maintenance prédictive pilotée par l'intelligence artificielle (IA) est peut-être l'un des avantages les plus significatifs des inspections automatisées. En analysant les données au fil du temps, les algorithmes d'IA peuvent prévoir quand et où la maintenance doit avoir lieu, en la programmant à des moments précis et en minimisant ainsi les interruptions inattendues.
- Cohérence : Les systèmes automatisés fournissent une évaluation régulière et objective de l'état des mines, réduisant ainsi l'erreur humaine et la variabilité des évaluations qui peuvent entraîner des oublis et des temps d'arrêt non planifiés.
Comment mettre en œuvre des inspections automatisées pour les puits de mine avec le scanner 3D Lazaruss ?
Pour mettre en œuvre efficacement les technologies d'inspection automatisée des puits de mine, les exploitants miniers doivent accepter de passer d'inspections plus traditionnelles à des systèmes automatisés avancés tels que le scanner 3D Lazaruss.
L'étape initiale de mise en œuvre comprend une analyse complète de la géométrie du puits de mine afin de s'assurer que les paramètres d'acquisition et la production répondent aux exigences de l'exploitant. Après cette analyse, notre équipe d'experts formera le personnel sur place afin qu'il puisse utiliser l'appareil facilement et efficacement. Le système est conçu pour s'intégrer rapidement et facilement dans l'exploitation de la mine, grâce à un système de fixation exclusif qui s'adapte à n'importe quelle taille de câble et dont l'installation ne prend que quelques minutes.
Une fois installé sur le câble, le scanner 3D Lazaruss fonctionne pratiquement sans intervention de l'opérateur. Il fournit à la demande des données à haute résolution qui permettent aux opérateurs miniers de prendre rapidement des décisions éclairées, réduisant ainsi les temps d'arrêt et améliorant l'efficacité opérationnelle.
Démonstration d'une réduction des temps d'arrêt
De plus en plus d'études de cas mettent en évidence l'efficacité des inspections automatisées des puits de mine pour réduire les temps d'arrêt imprévus. Par exemple, les partenaires de Point Laz qui ont intégré leur solution ont été en mesure d'évaluer l'alignement des guides dans le puits de mine et d'effectuer une maintenance prédictive aux endroits identifiés par le scanner Lazaruss. D'autres utilisateurs ont pu détecter la formation précoce de fissures dans le béton et intervenir avant que des dommages structurels ne se produisent en utilisant la complémentarité des mesures 3D et des informations visuelles disponibles.
En adoptant des technologies d'inspection automatisées, les exploitations minières peuvent réduire considérablement les risques associés aux temps d'arrêt imprévus. L'intégration de ces technologies s'avère rapidement indispensable pour les exploitations minières modernes qui s'efforcent de maintenir une efficacité et une productivité élevées dans un environnement industriel de plus en plus difficile.
Conclusion
L'adoption de technologies d'inspection automatisée des puits de mine telles que le scanner 3D Lazaruss offre une solution prometteuse à l'un des défis perpétuels de l'industrie minière : réduire les temps d'arrêt tout en améliorant la sécurité des mineurs. En exploitant la puissance de l'IA et de l'analyse des données, les mines pourraient non seulement minimiser les perturbations opérationnelles causées par les méthodes d'inspection traditionnelles, mais aussi améliorer leur sécurité et leur efficacité globale. Alors que l'industrie continue d'évoluer, l'intégration de ces technologies contribuera sans aucun doute à façonner l'avenir de l'exploitation minière, en débloquant l'efficacité et en garantissant la durabilité des opérations pour les années à venir.
Références
Benecke, N., Hancock, P. et Weber, M. (2016). Derniers développements dans la pratique de l'inspection des puits. Mine Surveying, 12-16. https://www.minesurveyors.com.au/files/ISM2016/Proceedings/Section3/1_N_Benecke.pdf
Boltstress (2018). Coût du temps d’arrêt dans l’industrie minière. https://www.boltstress.com.au/blog/webpage-content/downtime-cost-in-a-mining-industry
Dold, B. (2020). Extraction d'éléments critiques et de minéraux industriels à partir de déchets miniers - La dernière étape de l'évolution vers la durabilité de l'humanité ? Journal of Geochemical Exploration, 219. https://doi.org/10.1016/j.gexplo.2020.106638
Green, JJ, Bosscha, P, Candy, L, et al. 2010. n robot peut-il améliorer la sécurité dans les mines ? 25th International Conference on CAD/CAM, Robotics and Factories of the Future (CARsFOF), CSIR International Convention Centre, Pretoria, 13-16 juillet 2010, pp. 13. https://www.researchgate.net/publication/228412143_Can_a_robot_improve_mine_safety
Maxontana, M. (2022, 21 juillet). Atténuer le coût et les dangers des temps d'arrêt dans l'exploitation minière. Insights by Adcorp. https://insights.adcorpgroup.com/mitigating-the-cost-and-perils-of-downtime-in-mining
N. S. Harish Kumar, R. P. Choudhary & Ch. S. N. Murthy. (2020) Model based reliability analysis of shovel - dumper system's mechanical failures used in the surface coal mine : a case study. Safety and Reliability 39:3-4, pages 215-229.
Williams, G. (2024) Réouverture du puits 11 d'Impala et reprise des activités après un incident tragique. Mining Magazine. https://www.miningmagazine.com/operations/news/4169659/impalas-shaft-set-reopen-operations-resume-tragic-incident
Adoptez l'avenir de l'exploitation minière avec les technologies Point Laz. En investissant dans l'automatisation, votre exploitation devrait connaître une réduction des temps d'arrêt, une amélioration de la sécurité et une augmentation de l'efficacité, ouvrant ainsi la voie à un avenir plus rentable et durable. Explorez les possibilités dès aujourd'hui et faites un pas vers la transformation de vos opérations minières.